
These will have to be dealt with as well, so be vigilant. Just keep your mindset on your goal, which is to fix the problem at hand, and the possibility that additional factors which were previously unseen, may pop up. In other words, don’t get so tied up in the problem, that you accidentally bypass factors that caused the problem. This means that your RCA must remain a dynamic process vs a static one. The end result is to reduce or eliminate the source of the primary problem, or root cause. This can help you in selecting the proper methodology to conduct your real root cause analysis when the time comes. If you are new to performing a root cause analysis, it can’t hurt to grab a notepad, jot down the above steps, and simply try to work things out on paper first, just to give you an idea of what you are looking for.
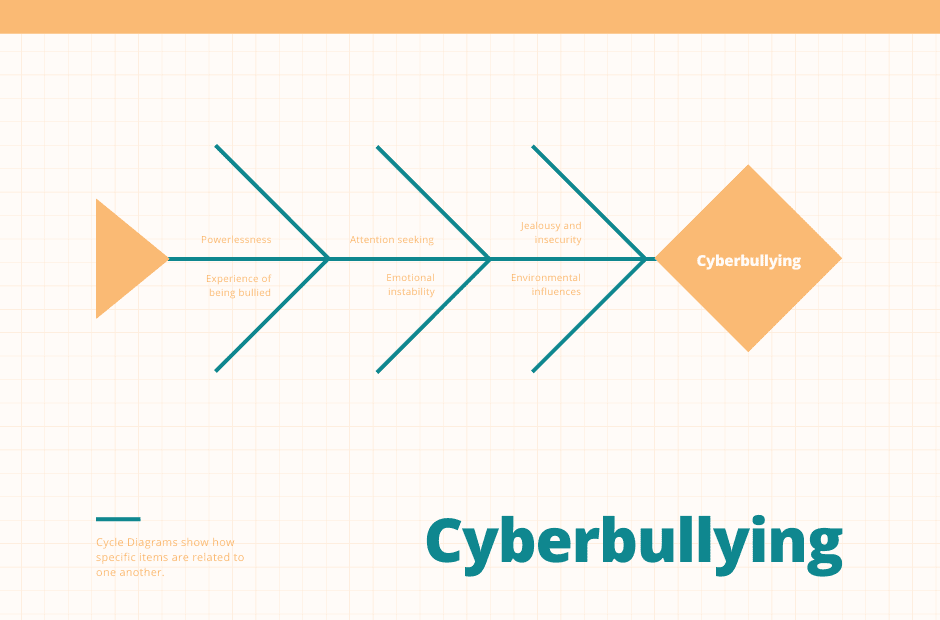

Once management has identified the root cause, it’s then time to choose an RCA technique to get rid of it. To ensure that this recurring underlying nightmare of cause and effect is eliminated, management employs Root Cause Analysis, or RCA to fix the problem. Failure of materials/manufacturing issue.When management repairs this underlying problem, or root cause successfully, there is very little chance of it returning, as all extenuating circumstances have been eliminated or reduced. Once the problem occurs, a root cause can usually be readily identified, and easily handled by the management. It’s referred to as a root cause because it’s been identified as the underlying reason for the problem at hand. A root cause refers to something in your business that is hindering your success.
